Phone: (+86) 13420084030 Email: info@qg-metal.com
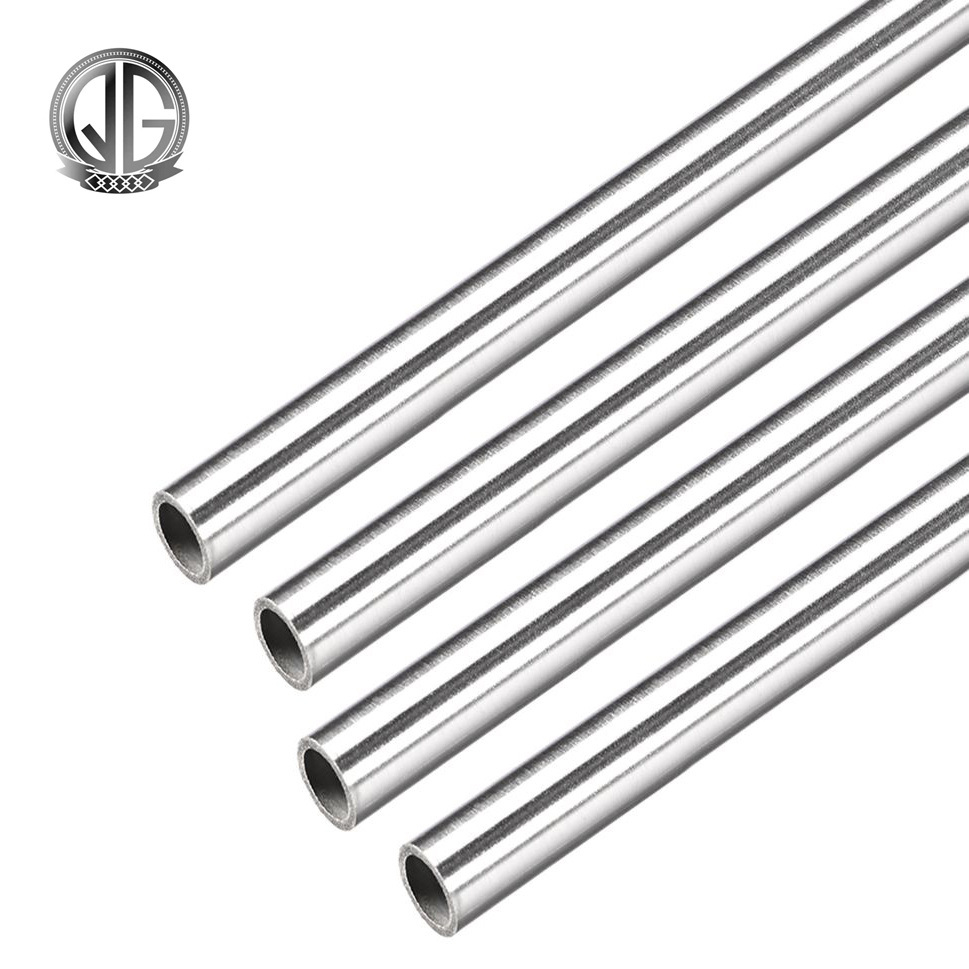
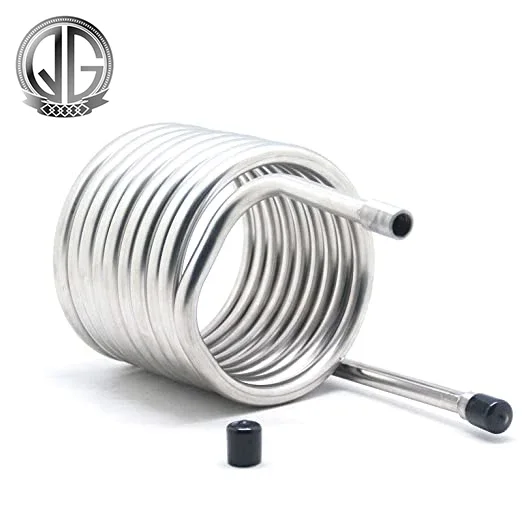
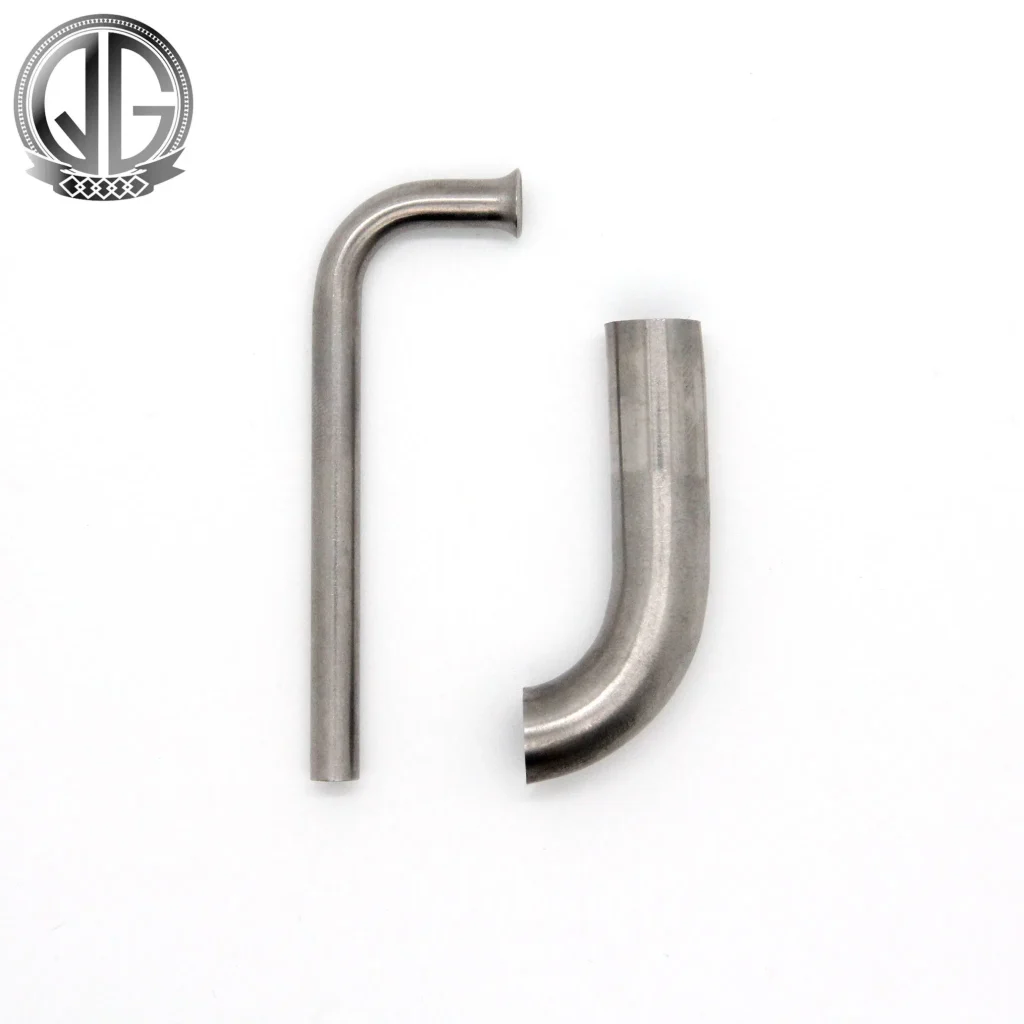
Metal Tube Processing
Metal tube processing is an integral part of modern manufacturing, enabling the production of components used across industries such as construction, automotive, aerospace, medical devices, and energy. The process involves a series of techniques to shape, cut, join, and finish metal tubes to meet specific design and functional requirements.
This article delves into the methods, applications, and innovations in metal tube processing, highlighting its significance in industrial and commercial production.
1. Overview of Metal Tubes
Metal tubes are hollow, cylindrical structures made from various metals such as steel, aluminum, copper, titanium, and alloys. Their properties—such as strength, lightweight nature, and corrosion resistance—make them indispensable for applications requiring structural support, fluid conveyance, or precision components.
Key characteristics of metal tubes include:
- Diameter and Thickness: Tubes can range from micro-diameters for medical uses to large-diameter pipes for industrial pipelines.
- Shape: While most tubes are circular, other profiles like square, rectangular, or oval shapes are also common.
2. Techniques in Metal Tube Processing
Metal tube processing encompasses various techniques that transform raw materials into finished components:
a. Tube Cutting
- Methods: Laser cutting, saw cutting, and abrasive cutting are commonly used to achieve precise lengths.
- Applications: Produces uniform sections for assembly or further processing.
b. Bending and Forming
- Processes: Mandrel bending, rotary draw bending, and roll forming are used to create curves and angles without compromising structural integrity.
- Use Cases: Essential for fabricating components like automotive exhaust systems, handlebars, and furniture frames.
c. Welding and Joining
- Techniques: TIG welding, MIG welding, and brazing join tubes to create complex assemblies.
- Industries: Widely used in construction, aerospace, and industrial machinery.
d. Drawing and Extrusion
- Description: Drawing involves pulling metal through a die to reduce its diameter, while extrusion pushes metal through a shaped die.
- Purpose: Creates seamless tubes with high dimensional accuracy and surface finish.
e. End Forming
- Methods: Swaging, flaring, and beading are employed to shape tube ends for specific applications, such as fittings or connections.
- Applications: Common in plumbing and hydraulic systems.
f. Surface Treatment
- Processes: Polishing, anodizing, and powder coating enhance corrosion resistance and aesthetics.
- Benefits: Extends the lifespan of metal tubes and improves their appearance.
3. Applications of Metal Tube Processing
Processed metal tubes are vital in a wide range of industries:
a. Construction
- Used in scaffolding, structural frameworks, and plumbing systems.
- Offers durability and strength for load-bearing applications.
b. Automotive
- Integral to exhaust systems, chassis components, and safety frames.
- Lightweight aluminum and high-strength steel tubes enhance fuel efficiency and safety.
c. Aerospace
- High-performance alloys are used in aircraft hydraulic systems, fuel lines, and structural supports.
- Demands precision and adherence to strict quality standards.
d. Medical Devices
- Micro-tubes are used in catheters, surgical instruments, and diagnostic equipment.
- Stainless steel and titanium are preferred for their biocompatibility.
e. Energy and Power
- Tubes are crucial for heat exchangers, boilers, and pipelines in power plants and oil refineries.
- Corrosion-resistant alloys ensure reliability in harsh environments.
4. Innovations in Metal Tube Processing
Technological advancements continue to revolutionize metal tube processing:
a. Laser Technology
- High-precision laser cutting and welding systems enhance productivity and accuracy.
- Enables complex geometries and clean cuts with minimal material wastage.
b. Automation and Robotics
- Robotic systems streamline tube handling, bending, and welding, improving efficiency and reducing human error.
- Automated quality control systems ensure consistency and adherence to specifications.
c. Additive Manufacturing (3D Printing)
- Although primarily used for prototyping, 3D printing metal tubes is gaining traction for customized, small-batch production.
- Offers unprecedented design flexibility.
d. Advanced Materials
- The development of new alloys and composites provides tubes with superior properties, such as lightweight strength and resistance to extreme temperatures.
5. Challenges in Metal Tube Processing
Despite its advancements, metal tube processing faces several challenges:
- Material Costs: High costs of raw materials and alloys can impact production expenses.
- Precision Requirements: Meeting tight tolerances and specifications demands sophisticated machinery and skilled operators.
- Environmental Impact: Processing metals can generate waste and emissions, necessitating sustainable practices.
6. Sustainable Practices in Tube Processing
As industries aim to minimize their environmental footprint, several sustainable practices are being adopted:
- Recycling: Utilizing scrap metal and reusing materials reduce waste and resource consumption.
- Energy Efficiency: Implementing energy-efficient machinery lowers power usage during production.
- Eco-Friendly Coatings: Switching to non-toxic coatings reduces environmental harm.
7. Conclusion
Metal tube processing is a cornerstone of modern manufacturing, enabling the creation of essential components for a wide range of applications. From intricate medical devices to robust structural frameworks, the versatility and adaptability of processed metal tubes are unmatched.
As technology evolves, innovations in automation, material science, and sustainability are shaping the future of metal tube processing. By addressing challenges and embracing advancements, this critical industry will continue to meet the demands of an ever-changing world, contributing to progress in engineering, healthcare, energy, and beyond.