Phone: (+86) 13420084030 Email: info@qg-metal.com
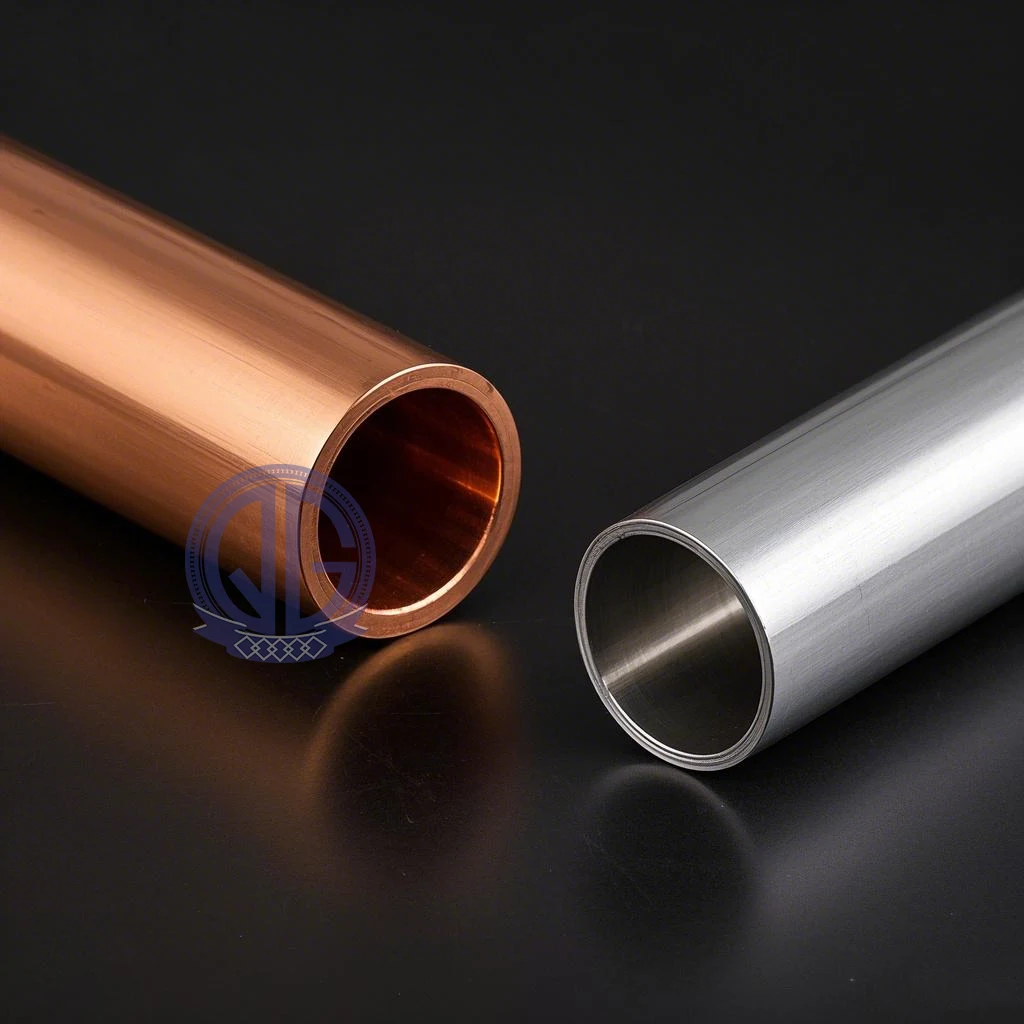
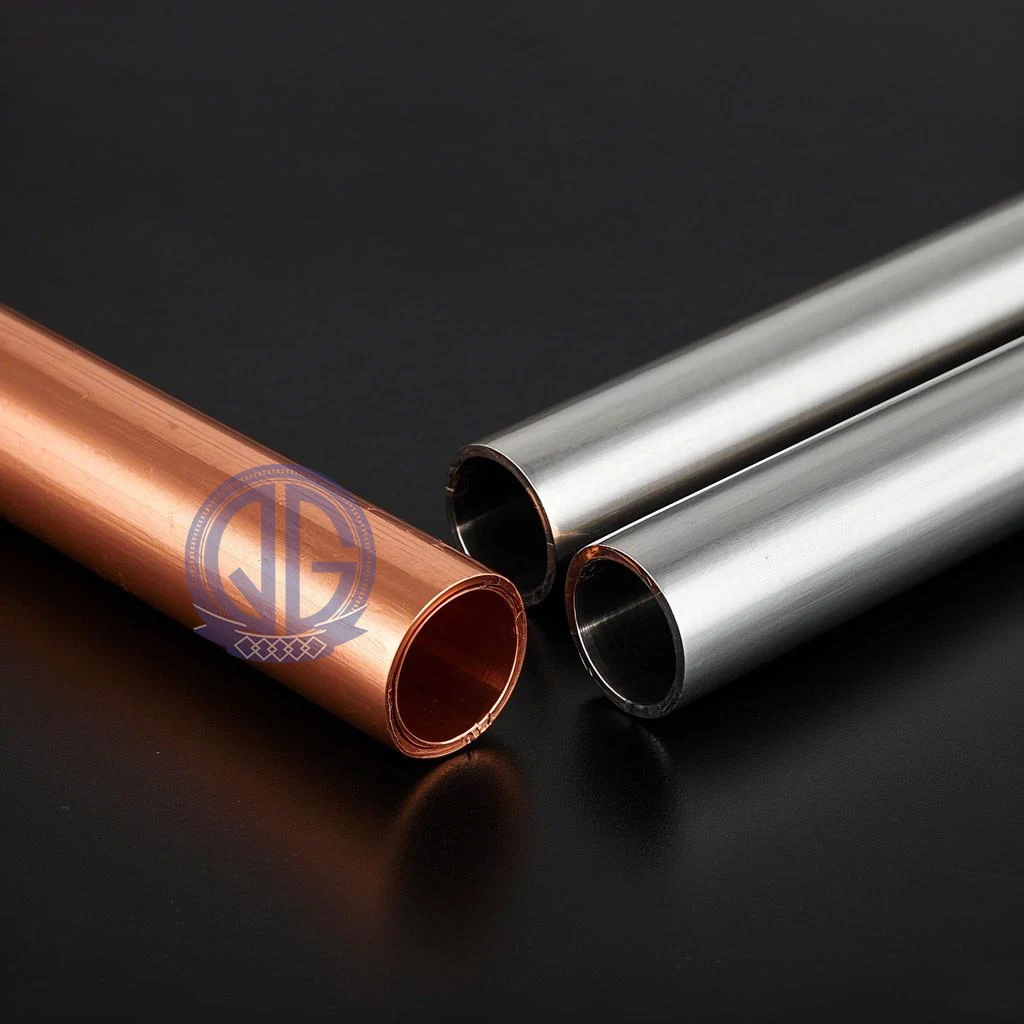
When it comes to tube flaring, the choice of material can significantly affect the process, the quality of the results, and the durability of the connections. Copper and aluminum are two of the most commonly used materials for tubing, each with its own advantages and disadvantages. But which one is better for flaring? Let’s explore this question in detail by examining their characteristics, applications, and suitability for flaring.
Understanding Tube Flaring
Tube flaring is a process of forming the end of a tube into a cone-shaped opening. This allows the tube to be securely connected to fittings or other components without leakage. Flaring is commonly used in HVAC systems, plumbing, automotive applications, and gas line installations. The success of flaring largely depends on the material of the tube, the quality of the tools, and the technique used.
Properties of Copper Tubes
Copper is a highly versatile and durable material widely used in various industries. Here are some key characteristics:
- Strength and Durability
Copper tubes are known for their excellent tensile strength and resistance to corrosion. This makes them ideal for long-term applications, especially in environments where exposure to moisture or chemicals is common. - Malleability
Copper is highly malleable, meaning it can be easily shaped without cracking or breaking. This property is particularly advantageous in flaring, as it allows for smooth and consistent results. - Thermal Conductivity
With high thermal conductivity, copper is often used in HVAC systems and refrigeration lines, where efficient heat transfer is critical. - Cost
Copper is generally more expensive than aluminum, which can be a limiting factor for budget-conscious projects.
Properties of Aluminum Tubes
Aluminum is a lightweight and cost-effective material that also sees extensive use in tubing applications. Its main features include:
- Lightweight
Aluminum is significantly lighter than copper, making it easier to handle and transport. This can be a major advantage in large-scale projects or installations requiring extensive tubing. - Corrosion Resistance
While not as corrosion-resistant as copper, aluminum performs well in most environments due to its natural oxide layer, which prevents further degradation. - Lower Strength
Compared to copper, aluminum has lower tensile strength and may be prone to cracking under stress, especially during flaring. - Affordability
Aluminum is considerably cheaper than copper, making it an attractive option for cost-sensitive projects.
Copper vs. Aluminum: Flaring Performance
- Ease of Flaring
Copper is easier to flare due to its malleability and ductility. It forms smooth and uniform flares that ensure a tight, leak-free connection. Aluminum, being more rigid and prone to cracking, requires extra care during the flaring process to avoid defects. - Tool Requirements
Flaring copper tubes can be done with standard tools, and the material’s softness ensures minimal wear on the equipment. Aluminum, on the other hand, may require specialized tools or additional lubrication to reduce the risk of cracking. - Durability of the Connection
Connections made with flared copper tubes tend to be more reliable and durable over time. Aluminum connections may weaken under stress or repeated thermal expansion and contraction. - Application Suitability
- HVAC and Refrigeration: Copper is the preferred choice due to its thermal conductivity and ability to handle high pressures.
- Automotive and Aerospace: Aluminum’s lightweight properties make it a suitable option, but only when stress levels are low.
- Plumbing and Gas Lines: Copper is generally favored for its long-term reliability.
Cost Considerations
While copper’s superior performance in flaring makes it the better choice for most applications, its higher cost can be a disadvantage for projects with tight budgets. Aluminum offers a more economical solution but often requires additional effort and precision to achieve satisfactory flaring results.
Environmental Impact
Copper mining and production have a higher environmental footprint compared to aluminum. For projects that prioritize sustainability, aluminum may be the more eco-friendly option, provided it meets the technical requirements.
Tips for Flaring Success
- Choose the Right Material
Consider the application, environmental conditions, and required durability when selecting between copper and aluminum. - Use High-Quality Tools
Invest in reliable flaring tools to ensure clean and accurate flares, regardless of the material. - Practice Proper Technique
Ensure the tube is cut cleanly and deburred before flaring. Apply adequate lubrication to minimize friction and reduce the risk of cracking. - Inspect the Flares
Always check the flared ends for cracks, uneven surfaces, or other defects before completing the connection.
Conclusion
When deciding between copper and aluminum tubes for flaring, the choice largely depends on the specific requirements of your project. Copper offers unmatched reliability, ease of flaring, and durability, making it the go-to material for most applications. However, aluminum can be a viable alternative for cost-sensitive projects or when weight reduction is a priority.
For high-pressure systems, critical connections, and environments demanding long-term durability, copper remains the superior option. On the other hand, aluminum can be a practical choice for less demanding applications where affordability and lightweight properties are more critical. By understanding the strengths and limitations of each material, you can make an informed decision and ensure the success of your flaring projects.